Responsibility for managing the cost and availability of Operations material through successful materials planning, stocking/signal strategy, production scheduling and commodity management. Develop strategies and performance metrics focused on timely support, development, and implementation of Lean Processes. Efficient operation of Receiving and the main Lean Supermarket is also under the management of the Director, SC. Measures of success include product OTD, supplier OTD, inventory DOS, Inventory Accuracy, material demand planning, and backlog management.

Position Responsibilities
This position interacts with all areas and levels of the company, using a multi-disciplinary approach to problem solving, and works to motivate team members toward the common goal, deliver perfect quality products to our customer on-time at lowest cost and inventory.
At the highest level, the role is accountable for establishing and implementing regional supply chain strategies to support evolving business requirements and global supply chain strategies in partnership with divisional, regional and external stakeholders.
Ensure both owned and 3PL distribution warehouses are sized, designed and staffed properly, in line with future requirements spanning volume, handing, storage, shipping and value-added service.
Balance supply and demand to achieve the optimal balance between worldwide inventory levels, plant operating efficiency and effectiveness, and on time delivery for the products served by the Niche Diagnostics Center of Excellence.
Responsible for ongoing management of Sales, Inventory and Operation Planning (SIOP) and for minimizing excess and obsolescence
Require routine, disciplined operational reviews that cascade through the organization to the warehouse floor, enabling rapid escalation of performance issues and objective evidence of strong performance to be rewarded.
Collaborate with senior leaders of major customers and internal stakeholders to provide outstanding service in line with their expectations.
Develops and maintains materials policy and procedures which assure timely delivery of goods, equipment, materials, and supplies, at the most economical cost, consistent with quality standards and specifications of the company
Apply Practical Process Improvement (PPI) tools and methods to manage materials control/order policies, finding opportunities to improve processes including the materials forecasts and order policy/lot sizes in order to effectively mirror our processes and anticipate material requirements while maintaining low inventory levels
Measure and implement metrics to generate data for decision making
Insures compliance with Quality Systems and applicable standards such as, FDA, ISO, IVDD and other regulatory requirements.
Manage the annual Performance Management and Development (PMD) and Human Resource Review (HRR) processes to maintain a robust staff that evolves into future leaders and is resilient to unexpected events.
Participate in Divisional, Regional, or Corporate Operations councils or forums to drive best practice sharing, benchmarking and talent development.
Guide Information System’s strategy and development for Supply Chain Operations, including Warehouse Management Systems (WMS), e-Commerce execution, Enterprise Resource Planning (ERP) and Transportation Management.
Require routine, disciplined operational reviews that cascade through the organization to the warehouse floor, enabling rapid escalation of performance issues and objective evidence of strong performance to be rewarded.
Evaluate spend and operating performance of our intercompany and finished goods outbound transportation lanes on a regular basis to assure performance is achieving stated goals and control thresholds.
Implement strategic programs to address evolving business requirements or issues, collaborating with our divisions, regions, carriers, freight forwarders, the Thermo Transportation Group (TTG) and other supply chain partners.
Participate in, if not lead, periodic bidding processes to re-quote the contracts with our carriers and other external transportation service providers, to achieve annual cost reduction targets.
Serve as a key functional leader across our Global Supply Chain to manage risk, proactively staying informed about potential geo-political issues and assuring contingencies are identified in advance of any real event.
Apply the Global Trade Compliance Policy across the region through direct or dotted-line reporting relationships with Site Leaders who are responsible for assuring development and implementation of procedures to ensure compliance with applicable global trade laws and regulations
Lead and facilitate PPI Steering Team, Sponsor Daily Senior Leadership Team Board, and drive PPI culture
Develop strategy to train and develop PPI experts
Develop Niche business process strategy and ensure maximizes the power of ERP platforms
Create and maintain data management process for ERP working closely with IT
Minimum Requirements/Qualifications
Bachelor’s Degree in Materials Management, Business Administration or related field or equivalent experience. Advanced degree such as MBA or Masters in Supply Chain Management is preferred.
10+ years of expertise in managing and developing staff in a supply chain and/or manufacturing operations environment is required, preferably with exposure to high volume, high mix, reagent, antibody and controls immunoassay products in an inter-disciplinary manufacturing environment.
Hands on experience using and specifying Inventory Planning & Control, Forecasting, Demand Planning, DRP (disaster recovery plan), replenishment, and warehouse management in ERP and best-of-breed software solutions is strongly preferred, with specific emphasis on SAP.
Exceptional supply chain optimization expertise and project management experience.
Exposure to global operations including but not limited to 3PL, international distribution, including packaging labeling, export documentation, duties, and regulatory approvals.
Thorough knowledge of a variety of laboratory chemicals and reagent manufacturing activities
Demonstrated background in the design and application of inventory planning and control systems emphasizing lean manufacturing and pull/Kanban principles
Experience in implementing or working with an effective continuous improvement i.e. LEAN, Six Sigma, etc., preferrably in material handling and warehouse management.
Practical understanding and experience with IT systems (ERP, MES, WMS etc.) Implementation /Invovlement with a SAP ERP project is preferred
Superior analytical and computer skills with experience utilizing analytical tools and databases along with an understanding of manufacturing (MPS/MRP)
Broad knowledge of P&L, Balance Sheet, NPV/ROI, and cost accounting principles.
Results oriented, metrics driven leader with a root cause, permanent fix approach, continuous improvement approach
Ability to effectively collaborate with peers in other functions and with colleagues in other businesses or divisions
CPM or APICS certification a plus
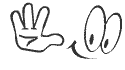