The Manager Facility Maintenance Plant provides technical direction and leadership to the Engineering group. Role ensures that the sites fixed assets are capable of performing and consistently fit for the purpose for which they were intended. The key being asset reliability and overall plant performance.
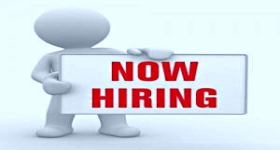
Management Responsibilities
•Define, propose and monitor the Maintenance and Improvement (M&I) plans and objectives in accordance with the Engineering Policy, Key Principles and the M&I Activity as outlined in the Nestlé Engineering Excellence (NEE) master document.
•Propose and implement work processes, procedures and technical resources related to the M&I team.
•Lead and coordinate the M&I team and maintain competencies, motivation and performance to achieve the M&I teams mission and objectives.
•Propose and control the M&I budget.
•Propose and monitor M&I in accordance with the key performance indicators.
•Build successful interaction between production and warehouse teams in equipment repairs and maintenance.
•Demonstrate and promote the company's values within the M&I team. Engineering team.
1. Functional Responsibilities
The functional responsibilities for a Maintenance Engineer are outlined within the NEE master document. The main responsibilities being to:
•Ensure that there exists within the M&I team an attitude of absolute intolerance for unsafe situations. That all team members are encouraged never to implement any change, whether directly instructed to, or under his/her own initiative, without first questioning its impact in relation to product safety/quality, people safety and the environment. No compromises should be tolerated.
•Ensure that the technical integrity and availability of equipment complies with all regulations.
•Ensure that Good Engineering Practices are being applied at all times.
•Ensure the implementation of all repairs/modifications resulting from gap assessments, plant audits and notifications.
•Ensure that all mechanics and operators receive direct on the line coaching in machinery and line operation skills in respect to the requirements of Hygienic engineering.
Responsibilities relating to the Nestlé Maintenance Strategy:
•Obtain managements support for M&I and ensure its alignment with the business strategy.
•Encourage close teamwork between all functions (Engineering, Production, Quality Management etc.).
•Review systematically all lines, processes and utilities that are critical to the business and those where failure can have an unacceptable impact on safety, environment or compliance with the law.
•Support and encourage the decentralizing of routine maintenance.
•Ensure that Continuous Improvement becomes a key pillar of the M&I culture.
•Implement Consequence Driven Maintenance (CDM) as the multi-discipline, team based approach to proactively maintain/improve the reliability and performance of the company's assets and Asset and Maintenance Management (AMM) as the process to manage the lifecycle of the fixed assets.
•Adopt the Maintenance Excellence vision by striving for the M&I "Proactive Domain".
Responsibilities relating to Consequence Driven Maintenance:
•Establish and manage the yearly, monthly, weekly maintenance plans to ensure essential maintenance is completed within a reasonable time.
•Monitor plant/equipment to ensure optimal operation and reduction of planned/unplanned downtime.
•Optimize Predictive Maintenance technologies (Condition Monitoring and inspections) to minimize unplanned downtime.
•Utilize Planned Downtime for Scheduled and Condition-Based Maintenance with Work Orders.
•Develop and implement improvements to minimize downtime for line change and cleaning.
•Liaise with Production, Quality Management on a daily basis to resolve technical and/or operational issues. (Stoppage Analysis from Downtime Reporting System).
•Establish with Production, shutdown and start-up work programs to minimize the risks to the product, people and production losses.
Responsibilities relating to Asset and Maintenance Management:
•Manage the technical stores, scheduled Work Orders, labor hour allocation and the equipment Bill of Material (BOM).
•Ensure that the job planning, material and services planning is accurate and effective.
•Ensure that the equipment history, damage code and root cause analysis are completed correctly.
Qualifications
REQUIREMENTS AND MINIMUM EDUCATION LEVEL:
B.S. degree in Engineering, preferably Mechanical or Electrical.
Minimum 3 years experience in a technical field, preferably in food manufacturing facility including maintenance responsibilities.
Supervisory experience in previous assignment.
EXPERIENCE:
In-depth knowledge of food processing equipment maintenance and technology.
Applicable maintenance techniques.
Appropriate maintenance execution.
Knowledge of food safety, regulatory requirements for food safety and hygienic engineering (OSH&R).
General understanding of financial analysis, budget reports and relevant business drivers.
AutoCAD view or Visio, CDM, AMM, ESAT, CIAT, NEMT, NEST etc.
SKILLS:
Strong technical and managerial skills.
Demonstrated leadership abilities.
Good interpersonal skills
Analytical skills in problem solving.
Excellent trouble shooting and problems solving skills in mechanical, electrical and PLC operating systems
Ability to perform under pressure and in ambiguous situations.
Strong organization and multi-tasking skills – ability to balance and prioritize several projects simultaneously.
Strong communication, presentation, and networking skills.
Proficiency in MS Office, MS Project
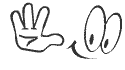
Send To A Friend