The Director of Supply Chain Optimization is a key position within Operations. The role has responsibility for analysing and mapping the supply chain footprint and for recommending and implementing opportunities to deliver supply chain optimization.
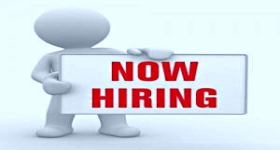
Key Duties and Responsibilities:
The Director of Supply Chain Optimization will achieve excellence in ensuring an optimized supply chain is in place balancing costs, service and inventory. Furthermore the role will look to evaluate capacity and capability to ensure the efficient flow of product to market. The role is divided between strategic orientation and operational execution as required. The role will be required to achieve the following deliverables including but not limited to:
1. Lead and Manage Direct Reports
Lead and manage direct reports, enabling an environment for continued high performance, including.
• Define team structure, role definition and talent development (including recruitment and succession planning)
• Define objectives setting and support to ensure delivery, providing day-to-day guidance to ensure operational execution
• Ensure key skills development against relevant competencies and identification of development requirements
• Facilitate the formal and informal feedback processes during calibration ensuring effective performance management
• Develop and implement Heineken cultural behaviours including ‘safety first’ as a priority
2. Supply Chain Strategy Definition
Support supply chain strategy definition for the different supply flows from breweries through to our distributor network.
• Define both short term and long term strategic planning to enable supply chain optimization (aligned with business strategy)
• Identify and develop alternate RTM solutions which create efficiencies, mitigate risk and enhance customer value
• Continually evaluate the end-to-end distribution footprint and implement agreed optimization initiatives
3. Vendor Management Strategy
Define vendor management strategy and opportunities to enhance capability and value with external suppliers.
• Develop a strategic approach to vendor management defining the right solutions for the business through an external network
• Oversee procurement strategy with external vendors, including ocean carriers, transportation and warehouse providers and any other vendors necessary to ensure effective supply chain operations
• Collaborate with other Operations stakeholders to develop the optimum solution to enable effective execution of logistics activities balancing cost, service and inventory
4. Capacity and Capability Planning
Develop capacity and capability planning to ensure the effective execution of the business.
• Define capacity and capability requirements for the logistics network building relevant insights from various stakeholders
• Model the impact of potential internal or external changes on the supply chain (Distributor, State, Volume, Logistics etc)
• Recommend relevant initiatives to improve capacity and mitigate any supply chain risk
• Ensure a cyclical planning cycle to manage the selling calendar and ensure appropriate capacity and capability is in place
5. Supply Chain Optimization and Improvement
Identify and implement improvement activities to enhance the supply chain.
• Undertake analytics (scenario planning, modelling, ‘what if’ etc) to ensure the effective management of supply chain flows
• Identify opportunities for supply chain improvement and work with all relevant parties to develop a relevant business case including cost savings, service improvements, complexity reductions etc
• Develop a Total Cost Management (TCM) enterprise, identifying and implementing agreed opportunities for cost optimization
6. Supply Chain Financial Management
Ensure effective financial planning and management control is in place to support supply chain activities.
• Oversee the supply chain budgeting and reporting cycle including the structuring, analysis and monitoring of all relevant logistics cost activities
• Provide input into financial planning and support the budget, latest estimate and monthly reporting cycle ensuring appropriate control and governance of all logistics costs activities
• Participate in vendor negotiation management for all external relationships ensuring value creation for the business. Collaboratively set negotiation strategy with Global Purchasing and define vendor allocation based on best overall risk / value proposition for HUSA
7. Performance Management
Deliver a culture of performance management and ensure delivery of agreed performance metrics.
• Define relevant KPI’s and success factors for logistics in conjunction with other stakeholders
• Agree performance targets to stretch the business, balancing inventory, cost and service to deliver sustained business value and Implement actions that will ensure achievement of performance metrics
• Provide a comprehensive and clear KPI reporting suite demonstrating performance levels and insights
• Implement a ‘review and resolve’ cycle to address any areas of sub-optimal performance, ensuring corrective action
• Create an environment of performance excellence within the Team
• Support a Total Productive Maintenance (TPM) approach to identifying and eliminating loss and waste within supply chain planning, utilizing relevant and appropriate business tools to drive improvements
8. Compliance and Governance
Ensure governance and compliance with all internal and external obligations for logistics management.
• Ensure clarity and compliance of all obligations including but not limited to Heineken policy, legal, statutory, FDA, etc
9. Other
Business Relationships
• Enable mutually beneficial business relationships through needs identification and the delivery of business requirements
• Collaborate with key business Stakeholders to Identify and resolve any critical issues impacting the business
• Includes both key internal and external relationships:
o Heineken USA – Key business functions including Operations, Sales, Marketing, Finance, Legal, Other
o Heineken Business Units – Global, Regional and Heineken supply relationships
o Distributors – Key relationships within the Distributor Network as appropriate
o Other Stakeholders – As required
Green Print behaviors:
• Put Safety First
• Act as an Entrepreneur
• Collaborate through Trust
• Focus on Support over Control
• Keep it Simple
• Learn, to Improve
Key Competencies and Skills:
The role requires an experienced and strong business leader with the necessary capabilities to ensure the successful delivery of the role requirements and deliver sustainable business value.
Role Profile
• Educated to Degree Level (Supply Chain, Manufacturing, Business, Finance or other relevant subject)
• 7+ years senior level experience in Operations / Supply Chain gained within the CPG Industry
• Extensive knowledge of supply chain modelling, optimization
• Experience of leading and motivating a high performance Team
Core Skills
• Strong supply chain analytical and modelling capability
• Problem solving skills
• Financial budget planning, analysis and reporting skills
• Strong communication and relationship skills
• Ability to write business reports and undertake presentations
• Ability to define, manage and deliver supply chain projects
• Ability to collaborate and work as a Team in a matrix organization
• Entrepreneurial approach with focus on continuous improvement
Other
• Knowledge of Alcoholic Beverages preferred
• Fully conversant in written and spoken English
• Knowledge of Excel and other relevant Supply Chain Optimization / Modelling Tools
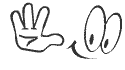
Send To A Friend