Develops and deploys the quality management system for the St. Paul and Birmingham sites. Assures systems and procedures for regulatory compliance are established and deployed. Periodically reviews the suitability and effectiveness of the quality system with executive management. Manages regulatory inspections.

Manages the entire Quality organization in a Class III device manufacturing facility and directs the department in support of division and/or company-wide initiatives. Quality functions include Laboratories, Compliance, Quality Operations, and Quality Engineering.
Responsible for results in terms of product quality and conformance to regulations and Baxter policies. Acts as the Management Representative for Quality.
Develops and deploys the quality system (e.g. management review, CAPA, design control, process control) that ensures products conform to defined requirements
Understands and deploys processes to assure conformance to regulations in a manufacturing plant. Manages regulatory inspections.
Periodically reviews the suitability and effectiveness of the quality system with executive management
Interacts frequently with all levels of internal management as well as across functions and business units
Manages interactions with customers and regulators concerning the quality of products, systems and processes
Identifies and manages continuous improvement projects that may span multiple functions or departments with the objective of achieving quality, reliability and cost improvements
Develops and adheres to the budget
Leads and develops people in supporting the change process to evolve the plants capabilities according to business needs
Manages overall coaching, training, development, and succession plans for the team
Partners with the Plant Manager and Facility Senior Leadership team to further develop the facility (improvement of processes, overall quality, risk profile, customer relationships, etc.)
A systems level leader, who operates at a systems level and considers how to most effectively balance quality, cost, people and service delivery to optimize Quality
Qualifications
Qualifications
In-depth knowledge of the regulatory environment for the manufacture of medical devices
Strong leadership skills and demonstrated success in multi-location teams
Demonstrated leadership around cultural and organizational change management
Strong, proven analytical and problem solving skills
Excellent and effective verbal and written communication skills
Verifiable success working with multifunctional, global teams
Excellent interpersonal communication, influencing, and negotiation skills required
Education and Experience
BS degree in Science or Engineering---an MS degree helpful
Minimum of 10 years related work experience in Quality, Manufacturing, or related field in a medical device setting—Class III preferred
7 years of management level experience
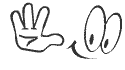