The Director of Operations leads the Production, Planning, Engineering/Maintenance, Shipping/Receiving groups to procure raw materials/packaging, schedule production and manufacture finished goods while optimizing safety, quality, customer service and working capital at an OSHA PSM covered Plant. Adherence to Henkel’s Safety, Health and Environmental (SHE) standards and ISO 9001, 14001 and OHSAS 18001 standards is maintained as the top priority, as is driving the Plant to achieve targets related to the business's Top Level Improvement Priorities.

Develop and manage the approved Plant budget to ensure adherence
Management of activities in the following areas:
Raw material, packaging, work in process inventory
Production cost for all finished goods
Quality of finished goods
In plant inventory levels (raw, packaging, WIP, finished goods)
Customer service levels (on time delivery, customer complaints and etc.)
Goals to meet or exceed plant safety performance standards
Production capacity and flexibility to handle various changed in production needs
Attainment of all Plant Operation Key Performance Indicators (KPI’s) – see below
Manage staffing levels - use of regular staff and temporaries to ensure availability of needed labor, without incurring overstaffing or understaffing costs
Capital Investment - prepare and present as needed the justification for capital equipment addition(s) to improve plant effectiveness/efficiencies and the overall footprint value of Henkel’s manufacturing capabilities.
Guide the implementation of and effective use of Henkel Production System (HPS) within the program delivery guidelines
Development and implementation of projects for equipment, process and people performance improvement in the areas of safety, product cost, delivery, and quality
Lead and/or participate in delivering the results of special individual or team projects as assigned by the VP of Operations
Drive improvements in the areas of Safety, Quality, Productivity, Service, and Inventory performance
Establish and maintain a personal presence on the shop floor - open an effective and positive culture of communications with all regular and temporary staff so that all employees are willing and able to communicate to the Director of Operations all suggestions, ideas, concerns and any other important information
Ensure that all employees have development plans established and there is proactive training and activities in place to ensure that all employees are incented to and take actions to reach his/her full potential as a Henkel employee
Manage all supervisory staff to ensure that objective, fair and honest performance evaluations and personnel improvement plans are developed and communicated in accordance with Henkel policy, or without delay when required.
Who We Are Looking For
Bachelor’s degree in Chemistry or Chemical Engineering, MBA a plus
Minimum ten years of experience in a manufacturing environment including five or more years of manufacturing supervisory/managerial experience
Outstanding verbal and written communication skills and demonstrated ability to communicate with all levels of the organization
Accomplished leadership skills that motivates staff at all levels to demonstrate behaviors that embrace a manufacturing culture that meets high performance standards, accepts and drives change, promotes a safety first work environment, team-work, mutual respect, integrity and respect for diversity
Expertise in the areas of Hazmat, Emergency Response, ISO 9001, ISO 14001, and OHSAS 18001, OSHA requirements including PSM
Excellent organizational. analytical and problem solving skills
Ability to handle sensitive information with confidentiality
Strong computer skills including excellent proficiency in Microsoft Office programs
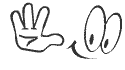